Pharmaceutical company improves OEE by 10% in 6 months by achieving maintenance excellence
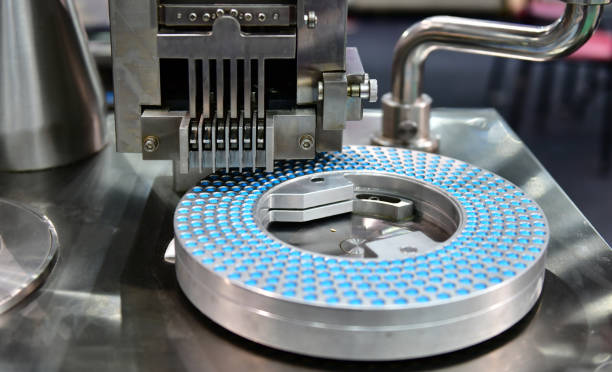
Sensor Data Management and digitalization for increased efficiency and ability to monitor machines. Thereby, improving maintenance practices and accomplishing business objectives.
Our client is one of the largest chemical producers in the world. They produce and supply raw materials for automotive, agricultural, chemical processing, oil and gas, cosmetics and processed food applications. They have a global presence, operate worldwide, and have a significant number of employees.
Initially, a lot of time had to be invested when gathering information about the sensors of one unit. Moreover, the plant had three units! This fact considerably reduced the time available for more productive tasks and, as a result, reduced productivity. Therefore, centralizing the data became a crucial aspect of the project.
The production site must meet the standards in order to operate
Furthermore, the production site must meet the required safety standards, such as GMISS (Global Mechanical Integrity and Safety Standard), in order to operate. We successfully met the standard practice to comply with GMISS regulations for our client. Any fluid with dangerous physical and chemical properties (acidity, toxicity, pressure, temperature, etc.) is considered as a part of GMISS.
Additionally, the presence of obsolete sensors, non-recorded data on these sensors, and the requirement to replace sensors necessitates manual identification and removal of the obsolete sensors and recording of corresponding data to ensure certainty. Obsolete sensors were involved in the installation, leading to malfunctions. They could not be replaced by identical ones due to the lack or incompleteness of precise sensor references.
Additionally, correcting the information of sensors to match the P&IDs based on the desired action set by the company is necessary. We also need to encode the information in the SAP so that it can be utilized.
Furthermore, to improve digitalization, it is necessary to register data in the database (SAP). As a part of the digitalization mission, ensuring the identification and registration of each sensor in the database optimizes the time allocated to searching for specific information about any plant sensors (up to 10 times faster than before).
Centralized access to the all the necessary information is crucial for maintenance and reliability best practices.
Furthermore, how our consultant worked on it: Taking the name plate of the sensors, putting it into Excel, and then transferring all the data into SAP while ensuring it was accessible by everyone.
To meet the required standard, basic knowledge of the GMISS regulation was needed. Furthermore, technical knowledge is needed for the identification of equipment.
Checking if the sensors were obsolete, and collecting and recording the data appropriately.
We identified the right sensor based on the present information and ensured a replacement. However, since prior to our cooperation there were no formal collections of information, figuring out the right information to use for replacement required electromechanical expertise and experience. Despite the manual approach being time-consuming to some extent, it ensures surety and paves the way for a solid base of data.
Analysing the P&Ids, subsequently finding the sensors based on the P&Ids to gather all the information and identify the obsolete sensors. Then, encoding the information into SAP through Excel, which had to be manually formulated.
Furthermore, identification of the sensors through the P&Ids and collecting the data, brand, reference, and serial no. is essential to establish a solid database that respects safety standards and enables access to all sensor data, resulting in improved maintenance practices.
Thanks to Otofacto, a solid database of the sensors of the plant is available to all the workers now. Identification of the location of the sensors will no longer require tedious inspection of P&Id diagrams.
The gains from Our approach towards recreation of the database in this way:
Since all the necessary data is easily and widely available, it enables our client to massively improve implementation time. The previous database has been doubled with about 700 sensors and 350 pictures uploaded to the SAP system. Consequently, sensors can be located up to 10 times faster through the SAP ERP system.
Thanks to the extensive knowledge and expertise of our consultant, the site is now entirely operational as the required standard GMISS (Global Mechanical Integrity and Safety Standard) is complied.
The digitalization and centralization of all the sensor data will allow the client to be more flexible, adaptable and spontaneous with the maintenance strategy. All the necessary information such as sensor spares parts, model, brand, and reference number etc enables the client to plan thoroughly and in advance. Leading to cost optimization and high productivity. Overall improving:
The digital overview of all the sensor data facilitates different teams within the organization to plan and strategize better.
Client’s maintenance and management strategies are now more proactive, they can now streamline their preventive maintenance processes:
The database provides a holistic view of asset health and enables data-driven decision-making to optimize overall effectiveness of maintenance strategies.
For example:
The faster access to all the sensor information brings immediate advantages for the maintenance team, the increased productivity directly translates to accomplishments of business objectives. In the long-run the database will enable preventive maintenance.
Preventive maintenance is a crucial stepping stone to achieve the greater industry 4.0 inspired firm.
Read our other success stories where we took this further and enabled a full fledged predictive maintenance production unit for our client, all in accordance with Pharma 4.0 initiative set by the ISPE.