Pharmaceutical company improves OEE by 10% in 6 months by achieving maintenance excellence
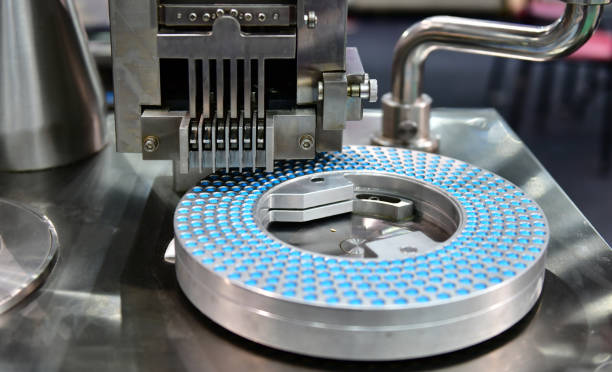
Downtime | Production efficiency | Artificial Intelligence | Predictive maintenance
How we ensured the longevity and efficiency of the equipment in order to perform predictive maintenance in metallurgy
Our client is a leader in the steel industry that operates both cold and hot rolling steel lines. With a production downtime of 67% and many untimely shutdowns, they needed our help to maintain their entire cold rolling steel production line on track and to optimize it in order to increase production efficiency.
To meet our client’s needs, we started by studying the production line entirely and detect the most frequent failures and defects. Then, we established and implemented optimized maintenance plans. Now we are looking to develop a predictive maintenance solution assisted by Artificial Intelligence (AI).
Our client has reduced machine downtime, wasted resources and costs while increasing the productivity and sustainability of its production units. Today, they will be able to continue gaining the highest return on critical assets by supporting predictive maintenance programs.