Pharmaceutical company improves OEE by 10% in 6 months by achieving maintenance excellence
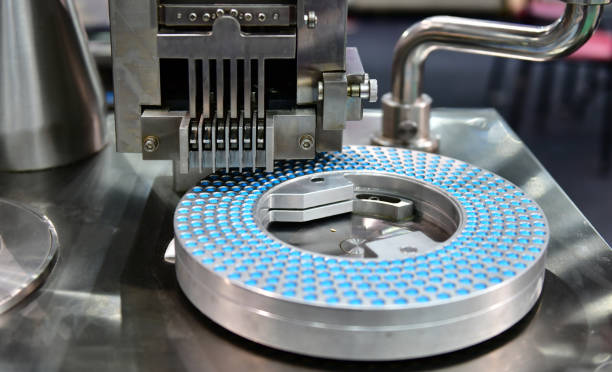
This transition allowed the client to set up a smart factory as per the Pharma 4.0 ™ initiative launched by the International Society for Pharmaceutical Engineering (ISPE).
The client is a multinational biopharmaceutical firm that required assistance setting up its new production unit in Belgium. This production unit had to be fully automated, according to the Pharma 4.0™ standards.
Most industrial sectors are experiencing a rapid advancement towards implementing industry 4.0 technologies. This leads to greater operational efficiency and increased competitive advantage. Pharmaceutical manufacturing is no exception to this trend.
The pharmaceutical industry is, however, subjected to much stricter regulatory laws. Thus, transformation to Pharma 4.0 ™ or smart factories is relatively slower and more complex.
We were able to meet the high standards of regulation in the pharmaceutical sector, such as the FDA and GMP regulations. Moreover, important requirements such as data integrity, documentation, and processes met the FDA regulatory compliance and the GMP practices authorization.
Furthermore, we helped the client to build the production unit from scratch and standardize the production and cleaning process (CIP). To add to that, the automation process and the evaluation of the automation code was done according to the ISA 88 regulation of automation.
The detailed solution-based approach to each challenge
To accomplish standardization, we built P&IDs to dictate exactly how each piece of equipment should function, interact, act, clean, produce, and sterilize. Moreover, we also helped to alter and improve the P&IDs until it met the client’s needs.
The approach adopted in building the automation was to break down the units into smaller, efficient, and manageable modules:
The units are, as a result, now fully automated. This method allows for a ground-up approach to the development and validation of the process for automation.
The automation was achieved, as per the FDA regulation for automation, highly recognized as the ISA 88 Standard for automation.
The two main advantages are:
Through the integration of Siemens PCS7, digital maturity was attained. More specifically, the production unit is now interconnected, monitored, fully automated, and controlled centrally.
FDS is a written document on the function of each automation philosophy. Since the project consisted of inputs from various suppliers, it was essential to constantly evaluate each process at play. Hence, sessions of RFIs (Responses for Information) were often organized for evaluation.
Furthermore, we assisted in bringing the various parties on the same level and building the framework for standardized automation for the entire production unit.
The 2nd aspect of the project in which we assisted the client was the cleaning. In the pharmaceutical industry, cleaning is a crucial part of the entire process. The vessels and pipes were, again, from different suppliers, but were all adjusted to have a common standard for cleaning purposes. Increasing cleaning efficiency and allowing the project to pass the ‘best cleaning practice‘ as per FDA regulations.
An example, is the ‘Caustic Standard’ pace. Standard pace advised by the FDA regulation.
Overall, reliable standardization and implementation of autonomous automating systems was achieved. The production unit, wholly interconnected with its processes streamlined!
Thus, leading to the following advantages:
To sum it up, the project allowed the client to attain digital maturity through increased control, laying the foundation to build future digital transformation strategies, which can potentially utilize other technologies from Industry 4.0.
Inevitably, due to the project, our client achieved a strong competitive edge thanks to the improved product quality, and reduced costs in the long run. Such an advantage is relatively difficult to accomplish in the pharmaceutical industry.