9 Common Challenges when implementing Operational Technology (OT) Systems
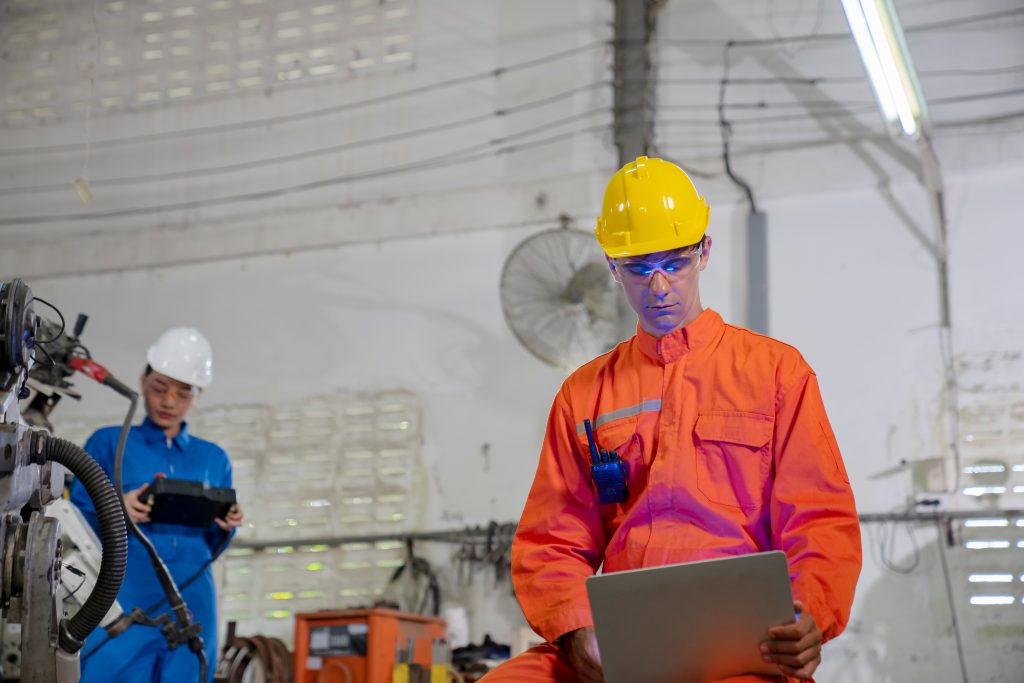
Implementing lean manufacturing? Think of its resilience and how lean industry 4.0 can play a major role!
It may be argued that world events can seriously hamper supply chains and cause massive disruptions. Nevertheless, according to studies, these events were not the core reason that prevented lean manufacturing from supporting properly the manufacturing companies, it’s their lack of resilience. This can be achieved with the right technology and the right Industry 4.0 roadmap.
Firms are facing various yet common challenges today, and this is where lean industry 4.0 comes in. In a perfect world, the supply chains would be secure, products and services would be available at will, and demand and supply would be perfectly balanced. However, companies have been faced by widespread disruptions in the aftermath of the COVID pandemic and other world events. This is hampering their ability to meet the world’s consumption demands.
Industries are naturally looking to stay competitive and profitable while providing the products and services that the customers expect. This raises the timeless question: how to produce with
Each company tries to find a balance in line with its strategy. Consequently, investments in industry 4.0 technologies come naturally to many, as Industry 4.0 precisely, supports these principles of lean manufacturing. Read more about Industry 4.0 technologies.
The competitive environment is accelerating, and the rate of development of new technologies is gaining momentum. Companies need to adapt and remain competitive.
A challenge as the complexity of the new systems for companies is increasing. What used to be purely mechanical now incorporates complex mechatronic systems with IoT as the new standard for any modern production plant.
They are also modern challenges, with the availability and variations of machines and products increasing, and the modern world becoming more connected and intertwined than ever before.
The use of lean manufacturing is not new in the scope of the modern industrial cycle and its use is nowadays widespread across different industries. The pursuit of the elimination of waste is integral to the strategy of all major manufacturers, and Lean industry 4.0 is the next evolution of this strategy.
How Lean industry 4.0 be the solution that addresses all these modern challenges?
In implementing a lean industry 4.0 strategy, a company is using the principles that the Toyota Production System famously introduced to the world. The elimination of waste necessitated the development of strategies such as “Just in Time” and “Just in Sequence”.
Pushing everyone in the supply chain, from the producer of raw material to final customer, to be more integrated with each other.
The world is moving away towards the pull model from a push model of production. In a pull model, production occurs only where and when required.
Lean industry 4.0 helps to minimize and eliminate waste in each of the following categories:
By searching for these elements, it becomes easier to identify areas to focus the attention where lean manufacturing can be applied.
Overall, industry 4.0 technologies improve interconnectivity, allow for a wholistic view and real-time overview, data-driven and intelligent operations. This improves visibility and – operationality on the whole supply chain. So, when an unprecedented event such as the COVID-19 pandemic hits, the link between the entire supply chain is unbroken and instead, flexible.
The implementation of lean manufacturing has shown tremendous potential in increasing efficiencies and cutting down on costs for manufactures. This enabled many to survive in the modern highly competitive environment. However, this does not come without a risk.
The shortages witnessed in the last 3 years have shown that the success of the model was dependent on the stability of the whole chain!
It is rare that so many factors occur at once. It should be, nevertheless, expected and planned for!
The core essence of the Toyota model has been misconstrued. Short-term saving dominated the industries’ priorities as they ignored the core of what made Toyota successful in becoming the largest Automotive manufacturer in the world.
Toyota stresses that the elimination of excess inventory is not the same as eliminating all inventory, that it uses production leveling to determine what to produce regardless of fluctuating short-term demands, and that it focused on training and building a workforce that is cross-functional and cohesive.
Ignoring what made Toyota so successful and only using the headlines of the lean principles lead to companies having a low resilience to disruptions in the supply chains.
Just like the core principles of lean manufacturing, implementation of industry 4.0 shouldn’t simply focus on short-term operational goals!
In order to take full the advantage of industry 4.0 a firm must implement “change management”. Furthermore, companies must focus on developing a clear and concise strategy roadmap aligned with their vision and mission and more importantly to their current state of the company. Doing that will make the implementation of Industry 4.0 far more fruitful.
For instance, when Siemens implemented AS/SR system (Automatic sorting and retrieval systems) replacing traditional conveyors, forklifts, and racks, the company had witnessed a staggering 60% reduction in required space and cost reduction of up to 40%.
With the implementation of Industry 4.0 new possibilities opened, when using, for example, predictive maintenance, industrial IoT, cloud computing, etc…
The access to real time data-driven solutions has pushed the boundaries of the detection of previously hidden waste and inefficiency. The era of the digital lean is here. However, only time will tell if industries repeat the same mistakes by only focusing on short-terms profits over long-term gains.
Solutions such as ERP, MES, SCADA and management systems all combine to provide a real time and data-driven approach to this problem. These systems work on different layers of the manufacturing processes. Starting with the shopfloor where breakdowns can be minimized or even avoided by using predictive maintenance.
Moreover, a SMART system is not just data acquisition and display. Smart systems enable decision-making based on data which is action-oriented. In addition, it derives actual business value. Digital lean helps in just that by using the industry 4.0 technologies.
This new era of lean helps companies form this lean strategy without compromising the robustness and resilience of their processes and supply chains.